Hướng dẫn thiết kế gia công CNC: Các quy tắc cơ bản giảm chi phí
Toc
- 1. Lợi ích thiết kế gia công CNC đối với khả năng sản xuất
- 2. Hướng dẫn thiết kế chung cho gia công CNC giúp giảm chi phí tối ưu
- 3. Thiết kế gia công đối với bộ phận khoan
- 4. Thiết kế gia công đối với bộ phận phay CNC
- 5. Thiết kế gia công đối với bộ phận tiện CNC
- 6. Những hạn chế ảnh hưởng đến thiết kế gia công CNC
- 7. Hướng dẫn lựa chọn vật liệu cho thiết kế gia công CNC
- 8. Bắt đầu dự án gia công CNC của bạn tại Cơ khí Intech
Hướng dẫn thiết kế gia công CNC: Các quy tắc cơ bản giảm chi phí
Hướng dẫn thiết kế cho gia công CNC là một khía cạnh quan trọng của quy trình sản xuất không nên bỏ qua. Bằng cách tập trung vào thiết kế của bộ phận, bạn có thể cải thiện đáng kể chất lượng và hiệu quả của quy trình sản xuất, giảm chi phí và tăng lợi nhu
Bằng cách làm theo hướng dẫn thiết kế gia công CNC đã thiết lập, bạn có thể sản xuất các bộ phận đáp ứng các thông số kỹ thuật và yêu cầu sản xuất mong muốn, đồng thời đảm bảo chất lượng và độ lặp lại cao. Cần có sự hiểu biết thấu đáo về các khả năng và hạn chế của máy móc để thiết kế các bộ phận cho gia công CNC.
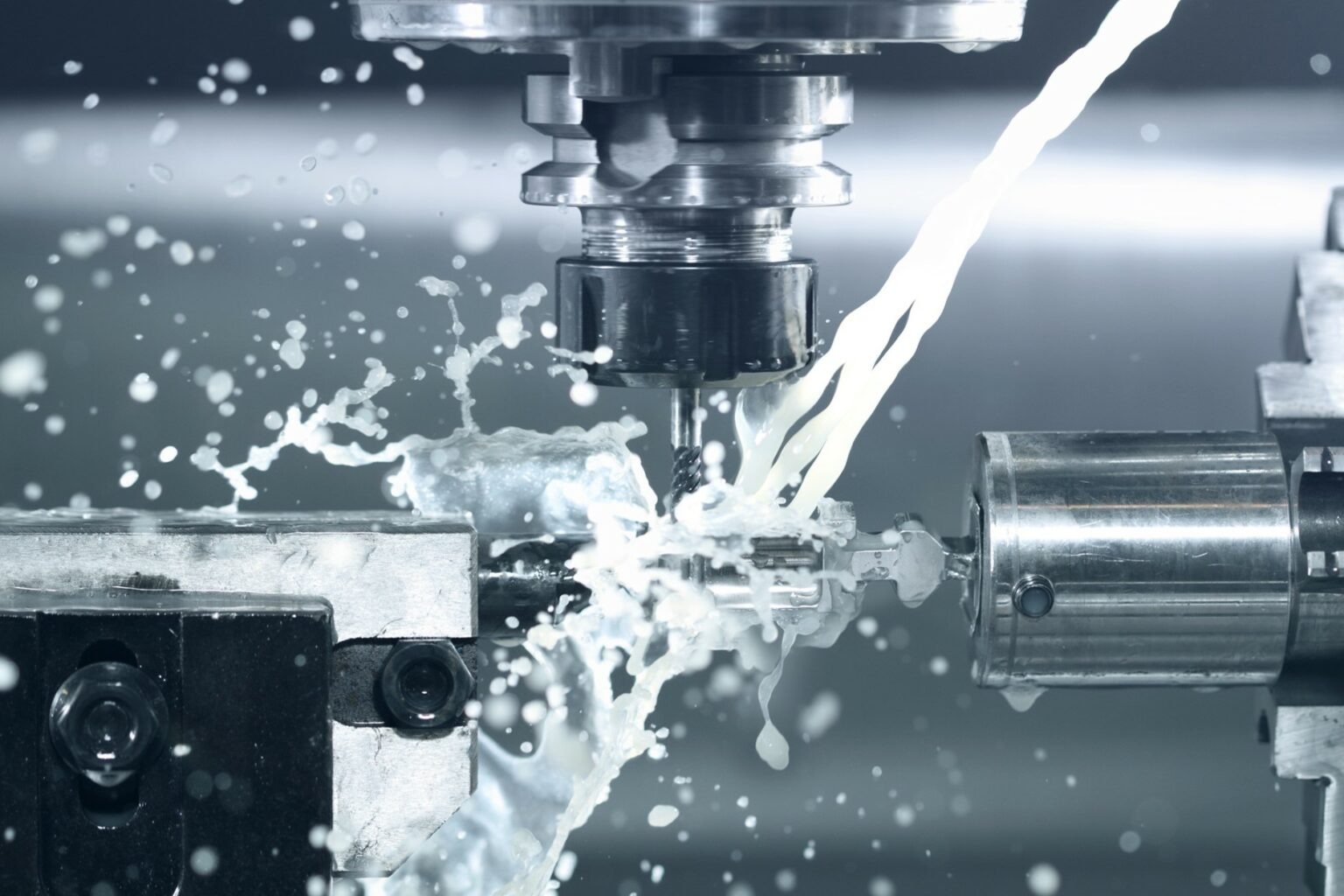
Lợi ích thiết kế gia công CNC đối với khả năng sản xuất
Thiết kế của một bộ phận là nền tảng của toàn bộ quy trình sản xuất và rất quan trọng đối với sự thành công của sản phẩm hoàn chỉnh. Giúp tối ưu hóa quy trình sản xuất, làm cho quy trình sản xuất nhanh hơn, hiệu quả hơn và tiết kiệm chi phí. Điều này thường yêu cầu sửa đổi các tính năng cụ thể không khả thi để sản xuất với các thiết bị và vật liệu sẵn có.
Một chiến lược thiết kế gia công CNC thành công mang lại những lợi thế sau:
– Giảm chi phí và thời gian sản xuất
Thiết kế của một bộ phận đóng một vai trò quan trọng trong việc xác định hiệu quả và tốc độ của quá trình sản xuất. Bằng cách xem xét các yếu tố như lựa chọn công cụ, thông số cắt và công suất máy, các nhà sản xuất có thể đảm bảo rằng quy trình sản xuất được tối ưu hóa về tốc độ và hiệu quả. Điều này có thể dẫn đến giảm thời gian chu kỳ, cải thiện năng suất và giảm chi phí sản xuất chung.
– Hợp lý hóa quy trình sản xuất một cách hiệu quả
Thiết kế của một bộ phận cũng có thể ảnh hưởng đến hiệu quả của máy CNC. Một bộ phận được thiết kế tốt có thể giảm thiểu hao mòn dụng cụ, giảm thời gian chu kỳ và tăng hiệu suất sử dụng máy, nâng cao năng suất và lợi nhuận. Thiết kế gia công CNC cũng đảm bảo tăng cường sử dụng vật liệu. Bằng cách tối ưu hóa việc sử dụng vật liệu, nhà sản xuất có thể giảm chi phí và tăng lợi nhuận.
Một bộ phận được thiết kế tốt sẽ giảm thiểu lãng phí vật liệu, điều này có thể tác động đáng kể đến chi phí sản xuất chung. Bằng cách xem xét các yếu tố như loại vật liệu, độ dày và hình dạng bộ phận, nhà sản xuất có thể đảm bảo rằng vật liệu được sử dụng hiệu quả và hiệu quả.
– Tránh các lỗi thiết kế nghiêm trọng
Việc sử dụng phần mềm CAD (Thiết kế được hỗ trợ bởi máy tính) và CAM (Sản xuất được hỗ trợ bởi máy tính) cho phép thay đổi nhanh chóng và dễ dàng đối với thiết kế của một bộ phận mà không cần thay đổi công cụ tốn kém. Tính linh hoạt này sẽ cho phép các nhà sản xuất phản ứng nhanh chóng với các yêu cầu thay đổi của khách hàng và thực hiện các thay đổi thiết kế khi cần thiết để cải thiện hiệu suất, chất lượng hoặc chi phí.
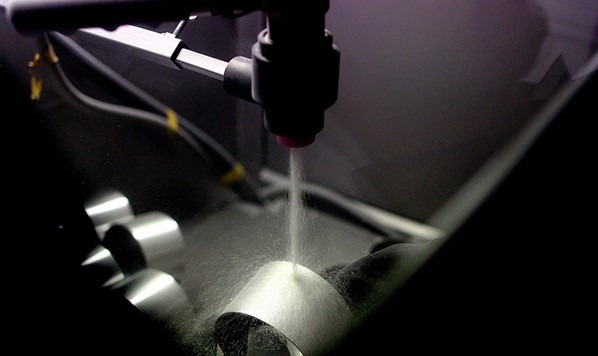
Hướng dẫn thiết kế chung cho gia công CNC giúp giảm chi phí tối ưu
Tuân thủ các nguyên tắc thiết kế nhất định có thể giảm chi phí liên quan đến gia công CNC trong khi vẫn duy trì tiêu chuẩn chất lượng và độ chính xác cao. Trong phần này, chúng ta sẽ khám phá các nguyên tắc thiết kế CNC khác nhau có thể được tích hợp vào quy trình thiết kế của bạn để giảm chi phí gia công CNC.
Sau đây là các thủ thuật và mẹo thiết kế cần thiết để giúp bạn tận dụng tối đa thiết kế dành cho gia công CNC:
– Chọn vật liệu mềm hơn
Một phương pháp thiết kế quan trọng để giảm chi phí gia công CNC là chọn vật liệu mềm hơn. Các vật liệu mềm hơn thường dễ gia công hơn, dẫn đến tốc độ cắt nhanh hơn và giảm hao mòn dụng cụ. Đổi lại, điều này có thể dẫn đến thời gian gia công ngắn hơn và chi phí thấp hơn.
Ngoài ra, các vật liệu mềm hơn thường ít bị nứt hoặc biến dạng hơn trong quá trình gia công, giúp cải thiện chất lượng chi tiết và giảm thời gian xử lý sau gia công. Tuy nhiên, điều quan trọng là phải xem xét mục đích sử dụng và ứng dụng cuối cùng của sản phẩm, vì các vật liệu mềm hơn có thể không phù hợp cho các ứng dụng chịu lực cao hoặc độ mài mòn cao.
– Giảm thiểu thay đổi công cụ và Thiết lập Workholding
Đây là một trong những hướng dẫn thiết kế gia công CNC quan trọng nhất có thể giảm đáng kể chi phí và thời gian thực hiện các hoạt động gia công của bạn. Càng nhiều thay đổi và thiết lập công cụ cần thiết trong một chu kỳ gia công, quy trình càng trở nên tốn thời gian và tốn kém hơn. Để giảm thiểu số lần thay đổi công cụ và thiết lập, hãy xem xét các phương pháp thiết kế sau:
- Thiết kế các bộ phận của bạn với các tính năng và hình học tương tự có thể được gia công bằng một công cụ duy nhất.
- Sử dụng các công cụ đa chức năng có thể thực hiện nhiều thao tác với một lần thay đổi công cụ.
- Giảm các thiết lập cần thiết bằng cách thiết kế các bộ phận có hướng nhất quán hoặc sử dụng đồ đạc mô-đun có thể chứa nhiều bộ phận.
– Tránh các bề mặt góc nghiêng và không phẳng
Các bề mặt góc nghiêng và không phẳng rất phức tạp và khó đối với máy, điều này có thể dẫn đến tốc độ cắt chậm hơn, thời gian gia công lâu hơn và tăng độ mài mòn của dụng cụ. Ngoài ra, các bề mặt này có thể gây khó khăn hơn để đạt được chất lượng bộ phận ổn định và dung sai chặt chẽ. Để tránh các bề mặt góc nghiêng và không phẳng trong thiết kế của bạn:
- Cân nhắc sử dụng hình học phẳng và đơn giản bất cứ khi nào có thể.
- Sử dụng các góc lượn và bán kính để làm mềm các góc nhọn và giảm số lượng các bề mặt phức tạp.
- Kết hợp các góc nháp vào thiết kế của bạn để cho phép loại bỏ vật liệu dễ dàng và giảm mài mòn dụng cụ trong quá trình gia công.
– Tăng kích thước của góc bên trong
Thực hành thiết kế đơn giản này có thể cải thiện đáng kể chất lượng và hiệu quả của các hoạt động gia công của bạn. Các góc bên trong là các góc được bo tròn hoặc các phần chuyển tiếp trong một bộ phận giúp giảm nồng độ ứng suất và cải thiện độ bền của bộ phận. Bằng cách tăng kích thước của các miếng phi lê này, bạn cũng có thể cải thiện quy trình gia công bằng cách:
- Giảm lực cắt và mài mòn dụng cụ trong quá trình gia công.
- Cải thiện loại bỏ chip và dòng vật liệu trong quá trình cắt.
- Giảm khả năng gãy dụng cụ và mài mòn dụng cụ sớm.
- Cải thiện bề mặt hoàn thiện và chất lượng một phần.
– Thêm đường cắt vào các góc nhọn
Đường cắt xén là các hốc hoặc rãnh ở các góc của một bộ phận cho phép tiếp cận công cụ tốt hơn và cải thiện khả năng loại bỏ vật liệu trong quá trình gia công. Chúng được sử dụng để:
- Giảm lực cắt và mài mòn dụng cụ.
- Cải thiện loại bỏ chip và dòng vật liệu trong quá trình cắt.
- Giảm khả năng gãy dụng cụ và mài mòn dụng cụ sớm.
- Cải thiện bề mặt hoàn thiện và chất lượng một phần.
Tuy nhiên, việc tạo các đường cắt dưới có thể là một nhiệm vụ phức tạp và đầy thách thức vì chúng có thể khó tiếp cận bằng các công cụ cắt tiêu chuẩn. Hơn nữa, các công cụ chuyên dụng hoặc gia công nhiều trục có thể được yêu cầu để gia công các đường cắt xén. Giảm thiểu kích thước và độ phức tạp của các đường gạch dưới có thể giúp đạt được kết quả tốt hơn.
– Sử dụng dung sai tiêu chuẩn
Trong gia công CNC, dung sai tiêu chuẩn được sử dụng để đảm bảo rằng chi tiết hoàn thiện đáp ứng các thông số kỹ thuật và yêu cầu chức năng mong muốn. Dung sai chặt chẽ không cần thiết có thể làm tăng chi phí và thời gian gia công. Bằng cách chỉ định dung sai dịch vụ gia công CNC tiêu chuẩn , các nhà sản xuất có thể giảm nhu cầu về các hoạt động phụ và nâng cao hiệu quả tổng thể của quy trình gia công.
Khuyến khích dung sai: ±0,1 mm, Khả thi: ±0,02 mm
– Văn bản và Chữ cái
Khi tạo văn bản hoặc chữ, công cụ phải có khả năng duy trì chiều rộng, chiều cao và khoảng cách không đổi trong suốt quá trình gia công. Bất kỳ thay đổi nào trong các yếu tố này đều có thể dẫn đến sản phẩm cuối cùng không đáp ứng các thông số kỹ thuật thiết kế.
Một vấn đề khác cần xem xét là phông chữ và kích thước của văn bản hoặc chữ cái. Nếu văn bản quá nhỏ, có thể khó đọc hoặc không đáp ứng các thông số kỹ thuật mong muốn. Nếu nó quá lớn, nó có thể gây ra hiện tượng lệch dao hoặc ảnh hưởng đến độ chính xác và độ chính xác của quá trình gia công.
Để giải quyết những thách thức này, bạn có thể sử dụng các phông chữ tiêu chuẩn rất phù hợp cho gia công CNC và tránh các ký tự quá phức tạp hoặc quá đẹp. Ngoài ra, bạn có thể chỉ định kích thước phông chữ lớn hơn và chọn phông chữ có chiều rộng, chiều cao và khoảng cách phù hợp hơn. Ngoài ra, điều cần thiết là phải xem xét cẩn thận hướng của văn bản so với phôi gia công và điều chỉnh công cụ cho phù hợp để duy trì chiều cao, khoảng cách và tốc độ cắt nhất quán.
– Kích thước phần
Một số loại máy CNC có khả năng khác nhau, bao gồm cả kích thước và công suất. Một số máy có thể quá nhỏ để chứa các bộ phận lớn, trong khi những máy khác có thể không xử lý được các bộ phận quá nhỏ. Do đó, các nhà thiết kế cần xem xét cẩn thận kích thước bộ phận và chọn máy phù hợp cho phù hợp.
Ngoài kích thước của máy, kích thước bộ phận cũng có thể ảnh hưởng đến tốc độ của quá trình gia công. Các bộ phận lớn hơn cần phải loại bỏ nhiều vật liệu hơn và mất nhiều thời gian hơn để gia công hơn các bộ phận nhỏ hơn. Điều này có nghĩa là thời gian gia công cho các bộ phận lớn hơn thường dài hơn và chi phí sản xuất cao hơn.

Thiết kế gia công đối với bộ phận khoan
Dưới đây là hướng dẫn thiết kế gia công cac bộ phận khoan CNC:
– Độ sâu lỗ tối ưu
Độ sâu lý tưởng của lỗ khoan phải cân bằng giữa độ ổn định của dụng cụ và độ bền của vật liệu được gia công. Khoan quá nông có thể dẫn đến mối nối yếu và giảm lực giữ của vít trong khi khoan quá sâu có thể khiến mũi khoan bị gãy hoặc cong, dẫn đến độ chính xác và độ hoàn thiện bề mặt kém.
Để xác định độ sâu lỗ tối ưu, bạn phải xem xét kích thước của mũi khoan, độ cứng và độ dày của vật liệu, độ bền cần thiết cho ứng dụng dự định và độ ổn định tổng thể của thiết lập máy. Nên khoan lỗ vừa đủ sâu để chứa vít hoặc dây buộc, để lại một số vật liệu để hỗ trợ. Nếu cần có mũi khoan, thì lỗ phải được khoan sâu hơn để có mũi khoan.
– Phân biệt lỗ xuyên và lỗ mù
Trong gia công CNC, hiểu được sự khác biệt giữa lỗ xuyên và lỗ mù là rất quan trọng, vì cả hai đều yêu cầu các công cụ và kỹ thuật khoan khác nhau. Lỗ xuyên suốt là một lỗ mở rộng hoàn toàn qua phôi từ đầu này sang đầu kia. Loại lỗ này thường dễ tạo hơn vì mũi khoan phải vào và ra khỏi chi tiết ở các phía đối diện nhau. Các lỗ xuyên qua có thể được sử dụng cho nhiều mục đích, bao gồm buộc, lắp và định tuyến các thành phần điện và cơ khí.
Mặt khác, các lỗ mù không đi hết phôi và dừng lại ở một độ sâu cụ thể. Các lỗ này thường được sử dụng để tạo các hốc, hốc hoặc túi trong phôi và thường khó sản xuất hơn so với các lỗ xuyên qua. Các lỗ mù yêu cầu hình học mũi khoan đặc biệt và tốc độ cắt để đảm bảo rằng lưỡi cắt không xuyên qua đáy của bộ phận.
– Tránh một phần lỗ
Lỗ một phần xảy ra khi mũi khoan không xuyên sâu hoàn toàn vào vật liệu và có thể do nhiều yếu tố gây ra như gãy mũi khoan, chọn mũi khoan không chính xác hoặc các thông số không chính xác như tốc độ, bước tiến và độ sâu cắt. Do đó, bạn nên chọn mũi khoan phù hợp, duy trì đúng thông số và sử dụng dung dịch làm mát để tản nhiệt.
– Tránh khoan qua lỗ sâu
Trong khi khoan, hãy nhớ rằng các lỗ giao nhau với các hốc hiện có trong các bộ phận có thể ảnh hưởng đến tính toàn vẹn cấu trúc của nó. Để tránh điều này, tốt nhất là đặt các điểm khoan cách xa các lỗ hổng hiện có. Tuy nhiên, nếu lỗ khoan phải đi qua khoang, hãy đảm bảo rằng trục tâm của nó không giao với nó để duy trì sự ổn định của bộ phận.
– Thiết kế kích thước mũi Khoan Tiêu Chuẩn
Tối ưu hóa thiết kế của bạn cho kích thước mũi khoan tiêu chuẩn để tiết kiệm thời gian và tiền bạc. Thiết kế cho các công cụ phổ biến sẽ giúp các cửa hàng máy móc sản xuất bộ phận của bạn dễ dàng hơn mà không cần dụng cụ tùy chỉnh tốn kém. Cân nhắc sử dụng kích thước mũi khoan tiêu chuẩn như 0,12 ”thay vì kích thước chính xác hơn nhưng ít phổ biến hơn như 0,123”. Ngoài ra, hãy cố gắng hạn chế số lượng kích cỡ mũi khoan khác nhau được sử dụng trong thiết kế của bạn, vì nhiều kích cỡ sẽ làm tăng thời gian và công sức cần thiết để thay đổi công cụ trong quá trình gia công.
– Chỉ định lỗ có ren
Một lỗ có ren cho phép gắn bu lông, vít và các ốc vít có ren khác. Đảm bảo chỉ định độ sâu chính xác của ren để dây buộc có ren có đủ độ ăn khớp để giữ các bộ phận lại với nhau. Sợi càng sâu, độ bám của dây buộc càng mạnh.
Loại vật liệu có thể ảnh hưởng đến loại chỉ. Vật liệu mềm có thể yêu cầu ren nông hơn, trong khi vật liệu cứng hơn có thể cần ren sâu hơn. Khi chỉ định các lỗ ren trong bản vẽ, hãy sử dụng chú thích ren rõ ràng và chính xác để đảm bảo tiêu chuẩn, cao độ và độ sâu của ren chính xác. Đảm bảo có đủ khoảng trống để lắp và tháo dây buộc có ren mà không buộc hoặc tước chỉ.
– Tránh chạm sâu
Để đạt được kết quả chính xác và chính xác, tránh chạm sâu là rất quan trọng trong thiết kế gia công CNC. Vòi càng dài, nguy cơ rung và lang thang trong khi hoạt động càng cao, dẫn đến sản phẩm cuối cùng không hoàn hảo. Một vòi vượt quá 3 lần đường kính của nó được coi là sâu và có thể gây ra thách thức đáng kể.
Tuy nhiên, trong nhiều trường hợp, ngay cả một lỗ ren có đường kính gấp 1,5 lần cũng sẽ cung cấp khả năng ăn khớp ren rộng rãi, do đó loại bỏ hoàn toàn nhu cầu sử dụng lỗ ren sâu. Sử dụng mũi taro sâu làm tăng nguy cơ gãy dụng cụ, sai sót ren và giảm độ chính xác, khiến nó trở thành khía cạnh không mong muốn của thiết kế gia công CNC.
Thiết kế gia công đối với bộ phận phay CNC
Dưới đây là hướng dẫn thiết kế trong gia công phay CNC:
– Ghi nhớ các dụng cụ cắt có sẵn
Thiết kế các bộ phận CNC có cân nhắc đến các công cụ phay CNC phổ biến có thể giảm chi phí và thời gian thực hiện. Bằng cách sử dụng các công cụ tiêu chuẩn và thiết kế theo kích thước tiêu chuẩn của chúng, bạn có thể giảm thiểu nhu cầu về các công cụ tùy chỉnh hoặc chuyên dụng.
Ví dụ, khi thiết kế các miếng phi lê bên trong, hãy đảm bảo bán kính không nhỏ hơn bán kính mà dụng cụ cắt tiêu chuẩn có thể xử lý. Mặt khác, việc thay đổi công cụ thành một công cụ nhỏ hơn sẽ là cần thiết để đạt được tính năng, điều này có thể không đáng để bỏ thêm thời gian và chi phí.
– Tránh các góc nhọn bên trong
Không thể thiết kế các bộ phận có các góc bên trong sắc nét bằng phay CNC, vì các công cụ tròn được sử dụng. Để tạo ra sự chuyển tiếp suôn sẻ, các góc có bán kính phải được kết hợp và bán kính phải lớn hơn đường kính của dao cắt. Kích thước của bán kính phải bằng một nửa đường kính của dụng cụ cắt.
– Tránh các khe sâu, hẹp
Chiều sâu cắt cuối cùng không được vượt quá các tỷ lệ nhất định dựa trên vật liệu được gia công. Ví dụ, với nhựa, tỷ lệ này không được lớn hơn 15 lần đường kính cối xay cuối, nhôm không quá 10 lần và giới hạn của thép là 5 lần. Điều này là do các dụng cụ dài hơn dễ bị lệch và rung hơn, dẫn đến bề mặt không hoàn hảo.
Hơn nữa, bán kính góc lượn bên trong cũng phụ thuộc vào đường kính của dụng cụ cắt. Nếu một rãnh rộng 0,55” cho một bộ phận thép được gia công bằng máy phay ngón 0,5”, thì độ sâu không được vượt quá 2,75”. Ngoài ra, các dao phay ngón có tỷ lệ chiều dài trên đường kính cao có thể khó kiếm hơn. Do đó, nên giảm độ sâu của rãnh hoặc tính năng hoặc tăng đường kính của dụng cụ cắt. Độ sâu khoang: 4 lần chiều rộng khoang.
– Thiết kế bán kính trong lớn nhất cho phép
Kích thước dụng cụ cắt được sử dụng trong phay CNC là một yếu tố quan trọng cần xem xét khi thiết kế bộ phận của bạn. Máy cắt lớn hơn loại bỏ nhiều vật liệu hơn trong một lần chạy, giảm thời gian và chi phí gia công. Để tận dụng tối đa khả năng của các máy cắt lớn hơn, hãy thiết kế các góc và miếng philê bên trong của bạn với bán kính lớn nhất có thể, tốt nhất là lớn hơn 0,8mm.
Một mẹo bổ sung là làm cho các miếng phi lê lớn hơn một chút so với bán kính của máy nghiền cuối, chẳng hạn như bán kính 3,3 mm thay vì 3,175 mm. Điều này tạo ra một đường cắt mượt mà hơn và tạo ra một kết thúc tốt hơn trên phần gia công của bạn.
– Chọn độ dày phù hợp
Điều quan trọng cần lưu ý là các thành mỏng trong các bộ phận có thể tạo ra những thách thức đáng kể trong quá trình gia công, đặc biệt là về việc duy trì độ cứng và độ chính xác của kích thước. Để tránh những khó khăn này, nên thiết kế các bức tường có độ dày tối thiểu là 0,25 mm đối với các bộ phận kim loại và 0,5 mm đối với các bộ phận bằng nhựa để chịu được sự khắc nghiệt của quá trình sản xuất.
Thiết kế gia công đối với bộ phận tiện CNC
Các hướng dẫn thiết kế gia công trong quá trình tiện CNC giúp bạn tiết kiệm chi phí:
– Tránh các góc nhọn bên trong
Các góc sắc nét bên trong và bên ngoài trong thiết kế một bộ phận có thể là một thách thức trong quá trình gia công. Để khắc phục vấn đề này, bạn nên có các góc bên trong có bán kính, cung cấp sự chuyển đổi dần dần để công cụ di chuyển trơn tru. Ngoài ra, việc kết hợp một góc nhỏ trong các thành bên dốc có thể loại bỏ các góc nhọn bên trong và đơn giản hóa quy trình gia công bằng cách giảm số lượng thao tác cần thiết với một công cụ duy nhất.
– Tránh các bộ phận tiện dài, mỏng
Sự không ổn định là một mối quan tâm chung khi nói đến các bộ phận dài và mỏng. Bộ phận kéo sợi có thể dễ dàng va vào dụng cụ, dẫn đến kết thúc không hoàn hảo. Để chống lại điều này, hãy xem xét kết hợp một mũi khoan tâm ở cuối và sử dụng một tâm để giữ cho bộ phận quay theo cách thẳng. Điều này có thể giúp duy trì sự ổn định và đạt được kết quả tốt hơn. Theo hướng dẫn, tốt nhất nên giữ tỷ lệ chiều dài trên đường kính bằng hoặc thấp hơn 8:1 để giảm thiểu rủi ro mất ổn định trong quá trình gia công.
– Tránh những thành mỏng
Khi tiện các bộ phận, điều quan trọng là phải lưu ý đến lượng vật liệu được gia công. Gia công quá mức có thể gây ra ứng suất quá mức trên bộ phận, trong khi các thành mỏng có thể dẫn đến giảm độ cứng và khó duy trì dung sai chặt chẽ. Theo hướng dẫn, độ dày thành của các bộ phận tiện phải được giữ ở mức tối thiểu 0,02 inch để đảm bảo độ ổn định và độ chính xác trong quá trình sản xuất.
Những hạn chế ảnh hưởng đến thiết kế gia công CNC
Gia công CNC là một phương pháp có độ chính xác và hiệu quả cao để sản xuất các bộ phận và linh kiện phức tạp. Tuy nhiên, giống như bất kỳ quy trình sản xuất nào, những hạn chế nhất định phải được xem xét khi thiết kế các bộ phận gia công CNC. Hiểu những hạn chế này có thể giúp đảm bảo rằng sản phẩm cuối cùng đáp ứng các thông số kỹ thuật cần thiết và quy trình sản xuất hiệu quả và tiết kiệm chi phí nhất có thể.
Những hạn chế đối với thiết kế gia công CNC bao gồm:
– Khả năng công cụ
Khi nói đến gia công CNC, một khía cạnh thường gây trở ngại là khả năng tiếp cận và chính xác các tính năng của máy với tỷ lệ chiều sâu trên chiều rộng lớn. Khả năng của công cụ và khả năng tiếp cận đóng một vai trò quan trọng trong việc xác định hình dạng nào có thể được gia công hiệu quả. Công cụ phải tiếp cận phôi gia công từ phía trên để loại bỏ vật liệu, gây khó khăn cho việc tiếp cận và gia công các tính năng phức tạp.
Ví dụ, các lỗ sâu có thể yêu cầu các công cụ có tầm với mở rộng để chạm tới đáy, điều này có thể làm tăng tiếng kêu của máy và giảm độ chính xác. Kích thước, hình dạng, khoảng cách di chuyển và các yếu tố khác góp phần tạo nên những hạn chế của gia công CNC và có thể ảnh hưởng đến độ chính xác của sản phẩm cuối cùng.
– Hình dạng công cụ
Khi nói đến gia công CNC, một khía cạnh quan trọng cần xem xét là hình dạng của dụng cụ cắt. Phần lớn các công cụ cắt CNC có dạng hình trụ và chiều dài cắt hạn chế, điều này ảnh hưởng đến đường cắt cuối cùng và hình dạng có thể đạt được.
Ví dụ, các góc bên trong của phôi gia công sẽ luôn có bán kính, ngay cả khi dụng cụ cắt được sử dụng là cực nhỏ. Điều này là do hình dạng của dụng cụ được chuyển vào bộ phận được gia công khi vật liệu được loại bỏ. Hình dạng hình trụ và chiều dài cắt hạn chế của các công cụ cắt CNC phổ biến, chẳng hạn như công cụ phay ngón và mũi khoan, cũng hạn chế khả năng gia công một số tính năng nhất định của chúng.
– Độ cứng của dụng cụ
Trong gia công CNC, dụng cụ cắt thường được làm từ vật liệu như cacbua, vonfram hoặc vật liệu tương tự có đặc tính vượt trội so với phôi. Mặc dù các đặc tính hiệu suất cao của các vật liệu này, độ lệch của dụng cụ vẫn có thể xảy ra và là nguyên nhân chính dẫn đến sai lệch trong thiết kế và kết quả cuối cùng.
Mặc dù làm việc với dung sai chung có thể không gây ra vấn đề gì, nhưng độ lệch nhẹ của dụng cụ có thể trở thành vấn đề quan trọng trong các công việc cực kỳ chính xác với dung sai chặt chẽ. Độ lệch gây ra bởi độ lệch của dụng cụ có thể hạn chế khả năng thiết kế và ảnh hưởng đến độ chính xác của sản phẩm cuối cùng.
– Độ cứng phôi
Các công cụ cắt CNC được biết đến với độ cứng đặc biệt và các đặc tính hiệu suất cao. Tuy nhiên, một số vật liệu phôi có thể tỏ ra là một thách thức, đặc biệt nếu chúng có các đặc tính cơ học vượt trội của riêng chúng.
Độ cứng của phôi có thể dẫn đến rung và lệch tác động tiêu cực đến độ chính xác và độ chính xác của các hoạt động gia công CNC. Độ chính xác và độ chính xác có thể đạt được với một phôi gia công cứng có thể khác nhau, khiến cho việc đáp ứng dung sai chặt chẽ trở nên khó khăn.
– Hình dạng phôi
Sự ổn định và thành công của quy trình gia công CNC phần lớn phụ thuộc vào hình dạng của phôi. Hình dạng của phôi là một yếu tố quan trọng quyết định số lượng quy trình cần thiết và khả năng tồn tại chung của thiết kế. Trong một số trường hợp, hình học phức tạp có thể yêu cầu định hướng lại trong quá trình gia công, ngay cả trên các máy nhiều trục. Những điều này có thể làm giảm hiệu quả tổng thể của quá trình.
Hướng dẫn lựa chọn vật liệu cho thiết kế gia công CNC
Lựa chọn vật liệu là một khía cạnh thiết yếu của hướng dẫn thiết kế gia công CNC. Các đặc tính của vật liệu sẽ ảnh hưởng đến khả năng gia công, chi phí và chất lượng tổng thể của chi tiết đã hoàn thiện. Khi chọn vật liệu gia công CNC, bạn phải xem xét khả năng gia công, tính chất cơ học, chi phí, tính khả dụng và tác động môi trường.
– Kim loại trong thiết kế gia công CNC
Kim loại được biết đến với độ bền và độ bền cao, khiến chúng trở nên lý tưởng để sử dụng trong các bộ phận được gia công bằng máy CNC chịu áp lực cao và tải trọng lớn. Chúng cũng có khả năng gia công tốt, chịu nhiệt và chống ăn mòn, và chúng rất linh hoạt trong việc sản xuất các bộ phận cho các ứng dụng khác nhau.
Một số kim loại phổ biến được sử dụng trong gia công CNC bao gồm: Nhôm, Thép, Thép không gỉ, Thau, Đồng, titan
– Nhựa trong thiết kế gia công cơ khí
Nhựa được sử dụng rộng rãi trong gia công CNC do chi phí thấp, trọng lượng nhẹ và khả năng đúc thành các hình dạng phức tạp. Một số loại nhựa cũng có khả năng kháng hóa chất tốt, khiến chúng trở nên lý tưởng để sử dụng trong các bộ phận sẽ tiếp xúc với hóa chất khắc nghiệt hoặc môi trường ăn mòn.
Một số loại nhựa phổ biến được sử dụng trong gia công CNC là: Acet (POM), Nylon, Polycarbonate (PC), Acrylic (PMMA), Polyphenylene Oxit (PPO), Polyetylen (PE)
Bắt đầu dự án gia công CNC của bạn tại Cơ khí Intech
Cơ khí Intech là nhà cung cấp dịch vụ gia công CNC đáng tin cậy, chúng tôi cam kết mang lại kết quả đặc biệt đáp ứng các tiêu chuẩn quốc tế. Ngoài ra, nền tảng sản xuất kỹ thuật số tiên tiến của chúng tôi mang đến trải nghiệm liền mạch cho những khách hàng muốn nhận báo giá tức thì cho các bộ phận CNC của họ.
Với sự kết hợp giữa tự động hóa và kiến thức chuyên môn, nền tảng của chúng tôi hợp lý hóa quy trình thiết kế và đảm bảo rằng mỗi bộ phận đều đáp ứng thông số kỹ thuật của khách hàng. Chúng tôi tự hào cung cấp trải nghiệm thiết kế gia công CNC toàn diện, dự đoán mọi thách thức sản xuất tiềm ẩn, cuối cùng mang lại kết quả chất lượng hàng đầu trong thời gian quay vòng ngắn nhất có thể.
Để đảm bảo kết quả tốt nhất, tốt nhất bạn nên làm việc với các chuyên gia gia công CNC giàu kinh nghiệm, những người có kiến thức và chuyên môn để thiết kế các bộ phận đáp ứng các tiêu chuẩn cao nhất. Liên hệ với Cơ khí Intech ngay hôm nay để bắt đầu dự án gia công CNC của bạn, Hotline: 0966 966 205
Bài viết liên quan:
- Hàn Laser là gì? Quy trình và các yếu tố ảnh hưởng Hàn Laser
- Các loại chất làm mát hiệu quả trong gia công CNC
- 7 mẹo và kỹ thuật gia công CNC tăng năng suất
thiet ke gia cong cnc thiet ke co khi thiet ke gia cong thiet ke cnc
Tin tức khác
-
Sự khác biệt Độ nhám bề mặt và độ hoàn thiện bề mặt trong gia công cơ khí
-
Cắt Plasma là gì? Ưu và nhược điểm cắt Plasma Kim Loại
-
Gia công Trục Xoay là gì? Các phương pháp sản xuất trục xoay phổ biến